Practice Makes Perfect for Our Fitters
Kwik Fit | Monday 7th July 2014 6:00pm
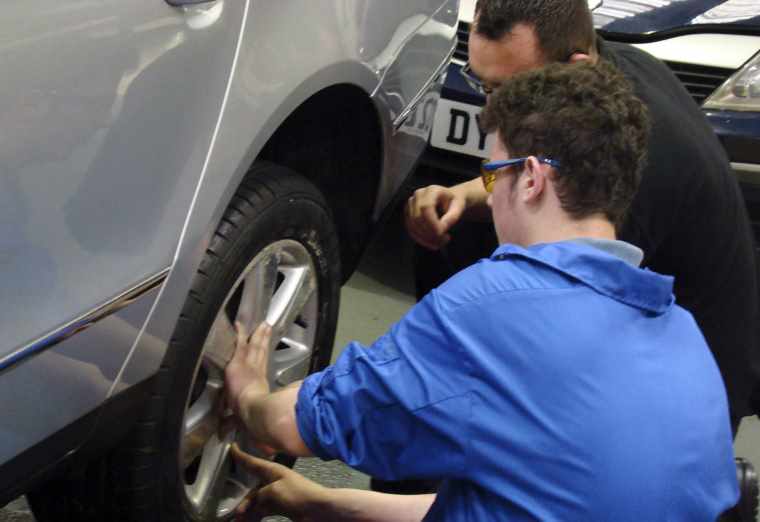
At Kwik Fit, we take staff training very seriously. It goes without saying that we would never let a member of our fitting team anywhere near your car without adequate and appropriate training - but we want to do more than that. We want you to be 100% satisfied with the work carried out on your car.
That’s why Kwik Fit provides 179,000 hours of staff training every year – that’s one week per year for every single member of in–centre staff.
State-of-the-art training facilities
Much of this training takes place at our five technical training centres across the UK where staff are taught advanced vehicle maintenance.
Our Derby facility is typical of these centres and features four classrooms and a large workshop area. On average, the centre runs 6 courses per week with 6 to 8 students in each class. Courses can last up to a week but generally the training team aims to get classes to spend 80% of the course in the workshop getting their hands dirty, with 20% classroom theory. This can vary, of course, depending on the training being given.
High-level qualifications
When we visited the centre, the training team was getting ready for a DVSA (formerly VOSA) vehicle systems course. This course prepares candidates for their DVSA qualification which is required to be permitted to carry out MOT tests in centre. Without the qualification, you simply carry out MOTs.
The course is heavily theory-based and sees the class complete 8 test exams throughout the week, preparing them for their real DVSA exam.
Tailored training
One interesting addition to the training centre classroom is the use of voting buttons. Kwik Fit’s trainers appreciate that we all learn at different speeds and may already have a degree of background knowledge in a given subject. Therefore, the voting buttons are used at the beginning of classroom sessions to gauge the existing knowledge of students.
If a basic knowledge of the subject is already possessed then the trainer can focus their time on areas where the class is less proficient. Essentially, each training session is tailored to the needs of the class.
Hands-on experience with test rigs
Outside of the classroom is where the technical training centre really comes into its own. At first glance, the workshop floor looks like any regular Kwik Fit workshop. There are a number of vehicles up on ramps and all the regular equipment you’d likely see, such as the Hunter wheel alignment machine and tyre fitting stations, all used to train staff in these staple Kwik Fit services.
Look a little closer though, and you’ll see it’s not just cars in the workshop but test rigs, parts of vehicles removed from their standard housing to enable training. These rigs include engines, braking systems and ignition systems, all used to simulate issues that can typically go wrong on a car. Kwik Fit has invested £750,000 on these specially created rigs alone because they are such an important part of our training process.
Let’s look at one example in particular – the changing of a timing belt. The workshop provides engine rigs from 11 of the most common vehicles owned in Britain, from the single cam, 8-valve Vauxhall Corsa to a more complex 3.0 litre, 24-valve Vauxhall Vectra engine with four camshafts. By working on the 11 rigs, the trainee gains enough knowledge to change the timing belt on any vehicle, regardless of the make. It is not until the trainees have completed the change on all 11 rigs that they are allowed to move onto the real vehicles in the training centre.
It's the same for all the test rigs in the centre; trainees must complete these simulations before being allowed to move onto real vehicles.
The diagnostic testing rig deserves special mention. Featuring a control box of 10 switches, the trainers can activate vehicle faults such as electrical failure or no fuel delivery at the flick of a switch. The switches can be set to any combination creating an endless number of fault scenarios for the trainees to correctly diagnose.
New course development
New courses are being developed all the time to ensure our staff all the time to ensure our staff are up-to-date with the latest developments in car maintenance.
But it’s not just the staff who are being tested — the technical training centres are a perfect place for us to try new equipment before launching new products into centres.
Over 4,500 members of Kwik Fit staff come through our training centres each year with nearly £1,000 being spent on training per employee per year – over twice the national average for the industry. So next time you bring your car in to see us for mechanical repairs, MOT, or just a tyre change, you can be rest assured that your vehicle will be in safe hands.
Any facts, figures and prices shown in our blog articles are correct at time of publication.
Featured Articles
Is it Illegal to Drive With One Headlight?
Saturday 19th July 2025
Wondering if it’s illegal to drive with one headlight? Learn about the safety risks and penalties of illegal blown bulbs and why you should fix them promptly.
Air Con in EVs & Hybrids: Experts Answer Your Questions
Monday 30th June 2025
Does air con drain EV batteries? Can you use the air con while charging an electric car? Find out the answers to these questions & more from Kwik Fit’s experts.
Why Is Your Car Making a Noise? Fixes & Tips
Friday 13th June 2025
When your car starts making unexpected noises, it can certainly be quite disconcerting; it may be nothing to worry about, but here’s what you need to know.